Stepper motors play a crucial role in various industries, providing precise control over rotational movements. Among the different types of stepper motors, the closed-loop stepper motor stands out for its advanced features and improved performance.
In this blog post, MXELECTRON will delve into the intricacies of closed-loop stepper motors, exploring how they work and the technology behind their precise motion control.
Understanding Stepper Motors
Before we dive into closed loop stepper motors, it’s essential to grasp the fundamentals of stepper motors in general. Stepper motors are electromechanical devices that convert electrical pulses into discrete mechanical movements, commonly referred to as steps. Each step corresponds to a fixed angular displacement, allowing for precise control in applications such as CNC machines, 3D printers, and robotics.
Basic Working Principle
Traditional stepper motors operate in an open-loop system, where the controller sends a sequence of pulses to the motor, and the motor moves accordingly. However, open-loop systems lack feedback mechanisms, making it challenging to detect errors or missed steps. Closed-loop stepper motors address this issue by incorporating a feedback system, enhancing accuracy and reliability.
The closed loop method, also known as sine commutation with field-oriented control using an encoder, relies on performance-adjusted current control and feedback of control signals. The encoder signals record rotor orientation, enabling the generation of sinusoidal phase currents in motor windings. Vector control of the magnetic field ensures the stator’s magnetic field is always perpendicular to the rotor’s, maintaining precise field strength for the desired torque. Controlled current in the windings produces a consistent motor force, resulting in a smoothly regulated motor.
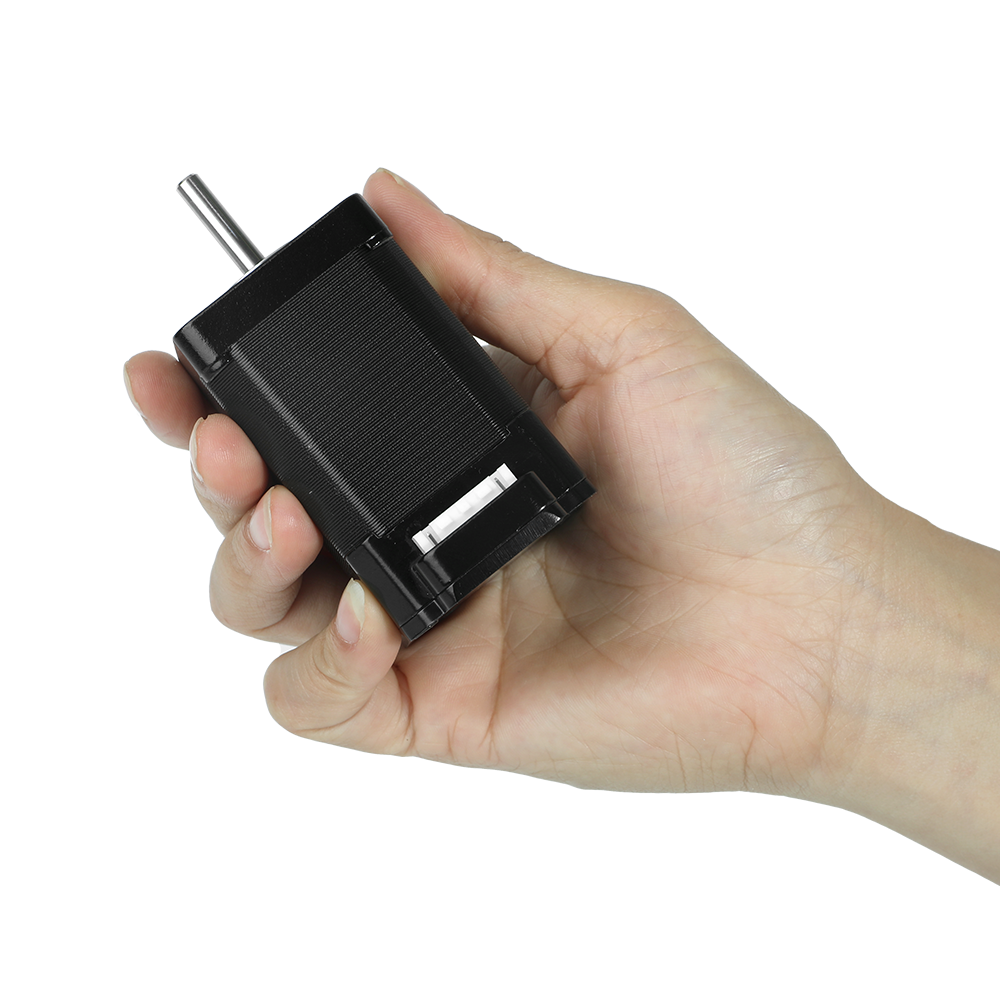
Closed-Loop Stepper Motor Architecture
Closed loop stepper motors consist of two main components: the stepper motor itself and a feedback device, typically an encoder. The encoder continuously monitors the motor’s actual position and provides feedback to the controller. This feedback loop allows the controller to make real-time adjustments to the motor’s operation, ensuring that it reaches the desired position accurately.
Working Method
- Position Detection: The encoder constantly measures the motor’s shaft position and sends this information to the controller.
- Comparison: The controller compares the actual position with the target position and determines if any deviation exists.
- Error Correction: If a deviation is detected, the controller adjusts the pulse sequence sent to the motor to correct the error and bring the motor back to the desired position.
- Continuous Monitoring: This process repeats in real time, ensuring that the motor’s position remains accurate throughout its operation.
Advantages of Closed-Loop Stepper Motors
Improved Accuracy: The closed loop system eliminates the issues of missed steps, providing precise control over the motor’s position.
Enhanced Torque at Higher Speeds: Closed loop stepper motors can operate at higher speeds without sacrificing torque, making them suitable for applications with dynamic requirements.
Reduced Heat Generation: The closed loop system optimizes motor performance, reducing heat generation and improving overall efficiency.
Error Detection and Recovery: The feedback system allows for the detection of errors and immediate correction, enhancing the reliability of closed-loop stepper motors.
Advanced Features of Closed-Loop Stepper Motors
- Adaptive Tuning
Closed loop stepper motors often feature adaptive tuning capabilities. This means that the control system can dynamically adjust parameters like current levels and step size based on the motor’s actual performance. Adaptive tuning optimizes the motor’s operation under varying conditions, ensuring efficient and reliable performance.
- Anti-Resonance Technology
Resonance is a common challenge in stepper motor applications, leading to vibrations and reduced performance. Closed loop stepper motors often incorporate anti-resonance technology, which actively suppresses resonance effects. This results in smoother motion, reduced noise, and improved overall system stability.
- Energy Efficiency
The closed-loop system contributes to energy efficiency by only supplying the necessary power to the motor. Traditional open-loop systems may continuously provide maximum current, leading to unnecessary heat generation and energy consumption. Closed loop stepper motors optimize power delivery, minimizing energy waste and reducing the need for elaborate cooling systems.
- Dynamic Torque Control
Closed-loop stepper motors excel in dynamic torque control, allowing precise adjustments to the motor’s torque output in real time. This feature is precious in applications with varying loads, accelerations, and decelerations. The closed-loop system ensures that the motor adapts swiftly to changes, maintaining optimal performance.
- Fault Detection and Safety
The feedback mechanism in closed-loop stepper motors enables the detection of faults such as overloads, over-temperature conditions, or mechanical obstructions. Upon detecting a fault, the controller can trigger safety measures or shut down the motor to prevent damage. This proactive approach enhances the overall safety and durability of the system.
Applications of Closed-Loop Stepper Motors
CNC Machining:
Closed loop stepper motors find extensive use in CNC (Computer Numerical Control) machining applications where precise control over tool movement is critical. The closed-loop system ensures accurate positioning of the cutting tool, resulting in high-quality and intricate machining.
3D Printing:
The additive manufacturing process in 3D printing demands precise control over the positioning of the print head or build platform. Closed-loop stepper motors excel in providing the required accuracy, contributing to the production of detailed and dimensionally accurate 3D-printed objects.
Laboratory Automation:
In laboratory equipment and automation systems, closed-loop stepper motors are employed for tasks that require precise positioning, such as sample handling, fluid dispensing, and analytical instrument movements.
Medical Devices:
Closed-loop stepper motors play a crucial role in various medical devices, including robotic-assisted surgery systems, where accurate and controlled movements are essential for surgical procedures.
Conclusion
Closed loop stepper motors represent a technological leap in motion control, offering a myriad of advanced features and applications across diverse industries.
As industries continue to embrace automation and demand higher precision, the adoption of closed-loop stepper motors is likely to grow, shaping the landscape of motion control in the future. Their ability to combine accuracy, efficiency, and safety makes them indispensable in applications where precision is paramount.