When it comes to selecting the right stepper motor for your application, the choice often boils down to understanding the specifications and differences between various models. Two popular options are the NEMA 17 and NEMA 23 closed loop stepper motors. In this article, we’ll delve into the key differences between these two types of motors, helping you make an informed decision for your next project.
What Is the Difference Between NEMA 17 and NEMA 23 Closed Loop Stepper Motor?
NEMA 17 motors are compact, cost-effective, and suitable for lighter tasks, while NEMA 23 motors offer higher torque and precision, ideal for more demanding applications.
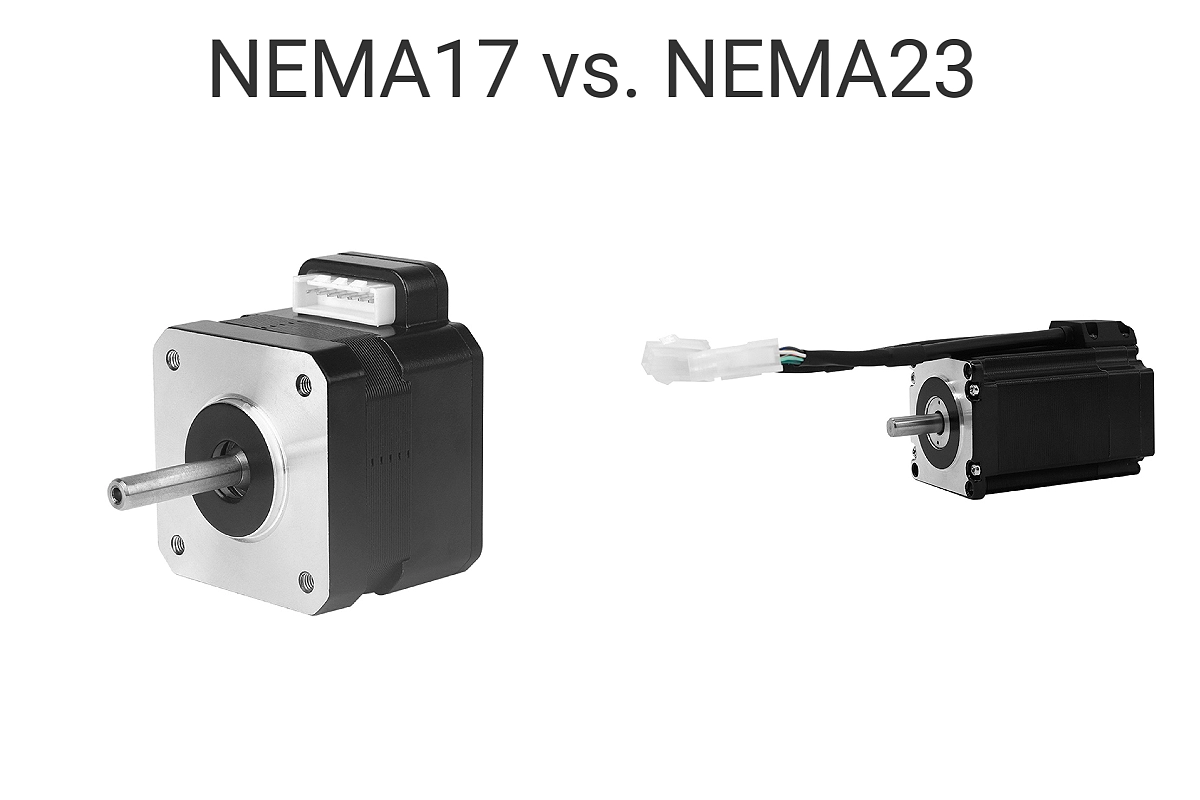
Key Differences Between NEMA 17 and NEMA 23 Closed Loop Stepper Motors
-
Size and Dimensions
The most noticeable difference between NEMA 17 and NEMA 23 stepper motors is their physical size.
The “NEMA” number refers to the faceplate size of the motor in inches:
NEMA 17: The faceplate is 1.7 inches (approximately 42mm) square.
NEMA 23: The faceplate is 2.3 inches (approximately 57mm) square.
This difference in size also impacts the overall length of the motor. NEMA 23 motors are generally longer, which can be a crucial factor when space constraints are a consideration.
-
Torque and Power
Torque is a critical factor in choosing a stepper motor, especially in applications requiring precise control and power. Typically:
NEMA 17: These motors provide less torque compared to NEMA 23. They usually offer torque in the range of 0.3 to 0.5 Nm (Newton meters).
NEMA 23: These motors offer significantly higher torque, usually in the range of 1.0 to 2.0 Nm.
The higher torque of NEMA 23 motors makes them suitable for heavier loads and applications requiring more force, such as CNC machines, 3D printers, and robotic arms.
-
Current and Voltage Requirements
The electrical requirements of the motors also vary:
NEMA 17: These motors typically operate at lower current ratings, around 1 to 2.5 Amps per phase. The voltage requirement is usually between 2 to 12 volts.
NEMA 23: These motors require higher current, generally ranging from 2 to 4 Amps per phase, and they operate at voltages between 12 to 48 volts.
Higher current and voltage ratings in NEMA 23 motors contribute to their increased torque and power.
-
Speed and Resolution
Closed loop stepper motors are known for their precision and control:
NEMA 17: They offer good speed and resolution, suitable for applications where moderate precision is acceptable.
NEMA 23: These motors provide higher resolution and can operate at higher speeds without losing steps, making them ideal for applications requiring high precision and quick movements.
-
Heat Dissipation
Heat dissipation is a factor that can affect the performance and longevity of stepper motors:
NEMA 17: Due to their smaller size and lower current requirements, they tend to generate less heat.
NEMA 23: With higher power and current, these motors can produce more heat, necessitating better heat management solutions like heatsinks or cooling fans.
-
Applications
Understanding where each motor excels can help in making the right choice:
NEMA 17: Ideal for applications with limited space and lower torque requirements, such as small 3D printers, light-duty CNC machines, and simple robotics.
NEMA 23: Suitable for more demanding applications with higher torque and precision needs, like industrial CNC machines, large 3D printers, and complex robotic systems.
-
Cost
Cost is always a consideration in any purchase decision:
NEMA 17: Generally more affordable due to their smaller size and lower power requirements.
NEMA 23: Higher in cost because of their enhanced capabilities and larger size. However, the increased performance can justify the higher price in many applications.
-
Integration with Existing Systems
NEMA 17: Due to their smaller size and lower power requirements, integrating NEMA 17 motors into existing systems is generally easier and more cost-effective. They are often compatible with a wide range of existing controllers and drivers.
NEMA 23: While NEMA 23 motors provide better performance, they may require more robust drivers and power supplies. Ensuring compatibility with existing systems is crucial, which might involve additional costs and modifications.
-
Maintenance and Durability
NEMA 17: With fewer components generating less heat, NEMA 17 motors tend to have lower maintenance requirements. However, they might not be as durable under heavy loads.
NEMA 23: These motors are built to handle more demanding applications and, as such, are generally more durable. However, the increased power and heat dissipation might necessitate regular maintenance to ensure optimal performance.
-
Noise and Vibration
NEMA 17: Typically produce less noise and vibration due to their smaller size and lower power. This makes them suitable for applications where a quieter operation is desired.
NEMA 23: Might generate more noise and vibration, particularly under high loads and speeds. Proper mounting and noise-damping techniques can mitigate these effects.
Making the Final Decision
When selecting between NEMA 17 and NEMA 23 closed-loop stepper motors, consider the following steps to ensure you make the best choice:
- Assess Your Load Requirements: Understand the torque and power needs of your application. Heavier loads and higher precision tasks generally necessitate the use of NEMA 23 motors.
- Evaluate Space Constraints: Determine the available space in your setup. If you have limited space, NEMA 17 might be the better option.
- Consider Electrical Specifications: Match the motor’s electrical requirements with your existing system. Ensure your drivers and power supplies are compatible.
- Analyze Heat Management Needs: Plan for adequate cooling if choosing NEMA 23 motors, especially for continuous high-load operations.
- Factor in Budget: Weigh the cost against the benefits of higher performance. Sometimes, investing in a more capable motor like the NEMA 23 can lead to long-term savings through improved efficiency and reduced downtime.
- Future-Proofing: Consider your future projects and scalability. Opting for a motor that might be slightly overkill for your current needs could save you from future upgrades.
Summary
NEMA 17 and NEMA 23 closed-loop stepper motors each have unique strengths and are suited to different applications. Understanding these differences, along with practical considerations such as integration, maintenance, and noise, will guide you to the best choice for your specific needs.
Frequently Asked Questions (FAQs)
Q: Can I replace a NEMA 17 motor with a NEMA 23 motor?
A: In many cases, yes, but you’ll need to ensure that your driver and power supply can handle the increased power requirements of the NEMA 23 motor. Also, consider the physical space and mounting compatibility.
Q: What applications are best suited for NEMA 17 motors?
A: NEMA 17 motors are ideal for applications like small 3D printers, light-duty CNC machines, simple robotics, and other projects where space is limited and high torque is not essential.
Q: Are NEMA 23 motors always better than NEMA 17 motors?
A: Not necessarily. The choice depends on your specific application requirements. While NEMA 23 motors offer higher torque and precision, they are also larger and more expensive. NEMA 17 motors are sufficient for many smaller, less demanding tasks.
Q: How do closed-loop stepper motors improve performance compared to open-loop motors?
A: Closed-loop stepper motors use feedback systems to correct positional errors, leading to higher accuracy, improved torque, and better overall performance. This makes them suitable for applications requiring precise control and reliability.
Q: What should I consider when installing a stepper motor?
A: Ensure proper alignment, secure mounting, adequate cooling (especially for NEMA 23 motors), and compatibility with your driver and power supply. Regular maintenance and monitoring for heat and vibration can also help maintain optimal performance.
Choosing the right stepper motor is crucial for the success of your project. By understanding the differences between NEMA 17 and NEMA 23 closed-loop stepper motors and considering your specific needs, you can make an informed decision that ensures optimal performance and longevity for your application.