Closed loop stepper motors are a fascinating component in the realm of motion control, offering precision and reliability in various industrial and automation applications. One of the critical aspects that engineers and enthusiasts often ponder is the maximum speed attainable by these motors. In this detailed guide, we’ll delve into the intricacies of closed loop stepper motors, exploring their capabilities, limitations, and factors influencing their maximum speed.
What Is the Maximum Speed of A Closed Loop Stepper Motor?
Generally speaking, the maximum velocity of a closed-loop stepper motor typically falls within a few hundred to several thousand revolutions per minute (RPM). A common figure is around 3000 RPM, although certain high-performance variants can attain speeds exceeding 10,000 RPM or even higher given optimal circumstances.
To provide some specific examples, let’s consider a few popular closed loop stepper motors and their maximum speeds:
*NEMA 23 Closed Loop Stepper Motor:
Maximum Speed: 3,000 RPM
NEMA 23 closed motor is commonly used in CNC machines, 3D printers, and other precision applications where accurate positioning is crucial.
*NEMA 34 Closed Loop Stepper Motor:
Maximum Speed: 2,500 RPM
With its larger size and higher torque output, this motor is suitable for larger machines and applications requiring more power.
*Integrated Closed Loop Stepper Motor and Driver:
Maximum Speed: 4,000 RPM
These compact units combine the stepper motor and driver into a single package, making them easy to integrate into various systems.
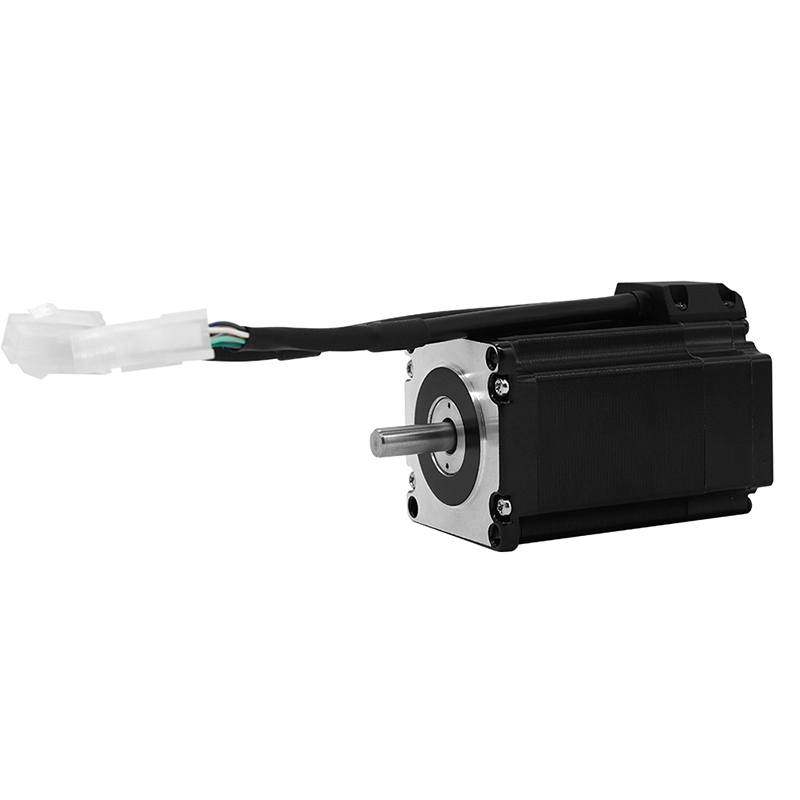
What does the Closed Loop Stepper Motor Maximum Speed Mean?
The maximum speed of a closed loop stepper motor refers to the highest rotational velocity it can achieve while maintaining stability and accuracy in positioning. This parameter is crucial in applications demanding rapid movements or high throughput.
What are the Factors Influencing Maximum Speed?
Numerous factors influence the maximum speed capabilities of closed loop stepper motors, including:
- Motor Design: The motor’s physical construction, such as rotor and stator design, can affect its speed capabilities.
- Drive Electronics: High-performance drive electronics are pivotal in maximizing motor speed and efficiency.
- Load Characteristics: Factors like inertia, friction, and torque requirements of the load influence the motor’s ability to attain higher speeds.
- Feedback System: The quality and responsiveness of the feedback system, typically encoders, significantly impact speed control and accuracy.
- Power Supply: A stable and adequate power supply is essential for consistent high-speed motor performance.
Applications Requiring High Speeds
Closed-loop stepper motors find applications in various industries where high-speed and precise motion control are paramount, including:
CNC Machining
3D Printing
Medical Devices
Robotics
Automated Manufacturing
How to Optimize Performance for Maximum Speed?
Engineers and system integrators can employ several strategies to optimize the performance of closed-loop stepper motors for maximum speed:
- Fine-Tuning Drive Parameters: Adjusting drive parameters such as acceleration, deceleration, and microstepping settings can enhance speed and responsiveness.
- Reducing Mechanical Inertia: Minimizing the inertia of moving components and optimizing mechanical design can improve the motor’s ability to accelerate and decelerate rapidly.
- Enhancing Cooling Systems: Efficient cooling mechanisms prevent overheating and ensure consistent performance, especially during prolonged operation at high speeds.
MXELECTRON’s Real Examples
We tailor a stepper motor for clients, where a closed loop stepper motor is deployed in a high-speed pick-and-place application. By implementing advanced drive algorithms and optimizing mechanical components, the system achieved up to 4000 RPM speeds while maintaining precise positioning, resulting in enhanced productivity and throughput.
FAQs (Frequently Asked Questions)
Q1: What are the advantages of closed loop stepper motors over traditional open loop systems?
A1: Closed loop stepper motors offer several advantages, including improved accuracy, reduced susceptibility to resonance, and enhanced dynamic performance, making them ideal for demanding motion control applications.
Q2: Can closed loop stepper motors be used in applications requiring continuous rotation?
A2: Yes, closed loop stepper motors can achieve continuous rotation by employing appropriate control strategies and feedback mechanisms to ensure seamless operation without losing steps or position accuracy.
Q3: Are closed loop stepper motors more expensive than open loop stepper motors?
A3: While closed loop stepper motors typically entail higher initial costs due to the inclusion of feedback systems, they often provide superior performance and reliability, resulting in lower overall operating costs and improved ROI (Return on Investment) in the long run.
Q4: How can I determine the maximum speed requirement for my application?
Determining the maximum speed requirement involves considering factors such as the desired throughput, cycle time, acceleration/deceleration profiles, and the inertia of the load. Conducting thorough testing and analysis is crucial to accurately assess the speed requirements and select an appropriate motor solution.
Q5: What maintenance practices are recommended for optimizing the performance of closed loop stepper motors?
Regular maintenance practices such as lubrication, inspection of mechanical components, and monitoring of feedback system performance are essential for ensuring optimal performance and longevity of closed loop stepper motors.
Q6: Does voltage affect closed loop stepper motor speed?
A6: Yes, the voltage does affect closed loop stepper motor speed.
Increasing the voltage supplied to the motor leads to a corresponding increase in speed. This relationship stems from the fact that higher voltage results in stronger electromagnetic forces within the motor, which facilitate faster movement of the rotor. However, it’s essential to strike a balance, as excessively high voltage can potentially lead to overheating and other adverse effects on the motor’s performance and longevity. Therefore, careful consideration and adjustment of voltage levels are necessary to optimize speed while ensuring the motor operates within safe parameters.
Q7: Can closed loop stepper motors operate in harsh environmental conditions?
A7: Closed loop stepper motors can be designed to withstand a wide range of environmental conditions, including temperature variations, humidity, dust, and vibrations, making them suitable for diverse industrial and outdoor applications.
Conclusion
In conclusion, understanding the maximum speed capabilities of closed loop stepper motors is crucial for optimizing performance and achieving desired outcomes in motion control applications. By exploring the intricacies of these advanced motor systems and implementing best practices for speed optimization, engineers and enthusiasts can unlock new possibilities in automation, robotics, and manufacturing. Embracing innovation and leveraging cutting-edge technologies will undoubtedly propel us toward a future where precision and speed converge seamlessly in the realm of motion control.
Welcome to contact us if you have any ideas!