As an engineer or a user of closed loop stepper motors, encountering issues where the motor vibrates but fails to turn can be frustrating and potentially detrimental to your projects. Understanding the reasons behind this problem and knowing how to solve it is crucial for efficient and effective motor operation. In this blog, we’ll explore the common causes of this issue and provide practical solutions to get your stepper motor back on track.
Reasons for closed loop stepper motor vibrating but not turning
A closed loop stepper motor may vibrate but not turn due to insufficient power supply, incorrect wiring, faulty driver, mechanical obstructions, resonance issues, overload protection, encoder feedback problems, incorrect motor parameters, poor grounding, and driver overheating. Addressing these issues can restore proper motor function.
-
Insufficient Power Supply
Reason:
One of the most common reasons for a vibrating but non-turning stepper motor is an insufficient power supply. closed loop stepper motors require a stable and adequate power supply to function correctly. If the power supply cannot deliver the necessary current and voltage, the motor may vibrate as it attempts to move but lacks the power to turn.
Solution:
– Check Power Supply Ratings: Ensure that the power supply meets the motor’s voltage and current requirements.
– Use a Dedicated Power Supply: If possible, use a dedicated power supply for your stepper motor to avoid fluctuations caused by sharing with other devices.
– Check Connections: Ensure all power supply connections are secure and free from corrosion or damage.
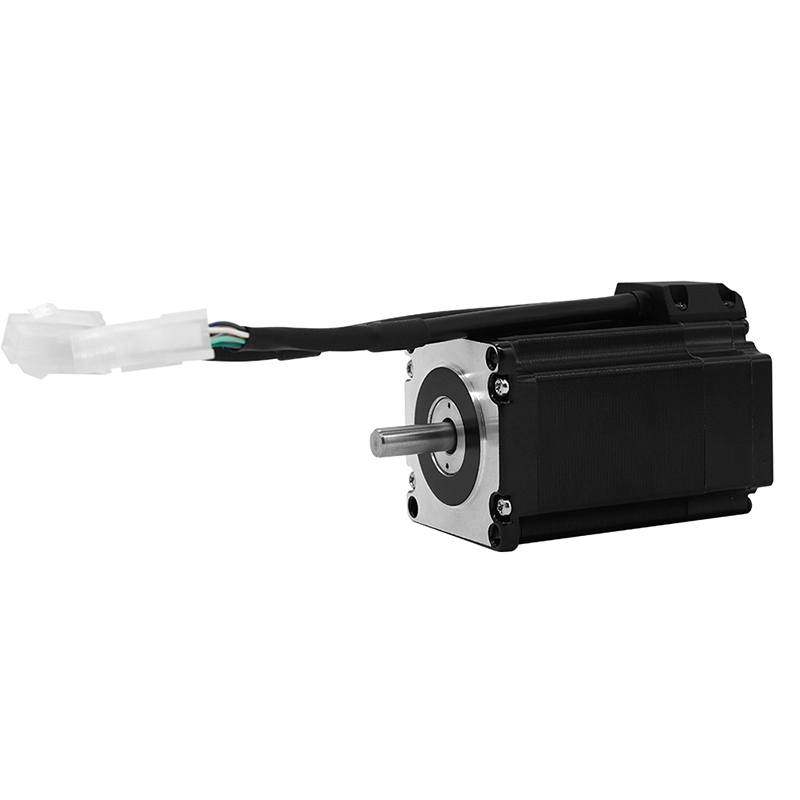
-
Incorrect Wiring
Reason:
Incorrect wiring can cause a stepper motor to vibrate without turning. Stepper motors rely on precise wiring to receive the correct signals from the driver. Any misconnection or loose wire can disrupt the motor’s operation.
Solution:
– Verify Wiring Diagram: Double-check the wiring diagram specific to your stepper motor model and ensure all connections are correct.
– Secure Connections: Make sure all wires are securely connected and not loose or frayed.
– Use Proper Connectors: Use appropriate connectors to ensure a reliable connection.
-
Faulty Driver
Reason:
The driver is responsible for sending the appropriate signals to the stepper motor. If the driver is faulty or not configured correctly, the motor may vibrate instead of turning.
Solution:
– Test the Driver: Use a known good driver to test if the issue persists.
– Update Firmware: Ensure the driver’s firmware is up to date.
– Check Driver Settings: Verify the settings on the driver, such as microstepping and current limits, are correctly configured for your motor.
-
Mechanical Obstruction
Reason:
A mechanical obstruction can physically prevent the motor from turning. This can be caused by debris, misalignment, or binding in the mechanical components connected to the motor.
Solution:
– Inspect for Obstructions: Carefully inspect the motor and connected components for any debris or foreign objects.
– Align Components: Ensure all mechanical components are properly aligned and not causing binding.
– Lubricate Moving Parts: Regularly lubricate moving parts to reduce friction and prevent binding.
-
Resonance Issues
Reason:
Stepper motors can suffer from resonance issues, especially at certain speeds. Resonance can cause excessive vibration and prevent the motor from turning effectively.
Solution:
– Adjust Speed: Try running the motor at different speeds to see if the vibration reduces or stops.
– Use Damping Techniques: Implement damping techniques such as adding rubber mounts or using a different mounting method to reduce vibration.
– Change Step Resolution: Adjust the micro stepping settings on the driver to change the step resolution, which can help mitigate resonance.
-
Overload or Overcurrent Protection
Reason:
Many stepper motor drivers have overload or overcurrent protection features. If the motor draws too much current, the driver may enter a protection mode, causing the motor to vibrate but not turn.
Solution:
– Check Current Settings: Verify that the current settings on the driver are appropriate for your motor.
– Reduce Load: Ensure the load on the motor is within the motor’s rated capacity.
– Monitor Temperature: Check for overheating issues and ensure adequate cooling for the motor and driver.
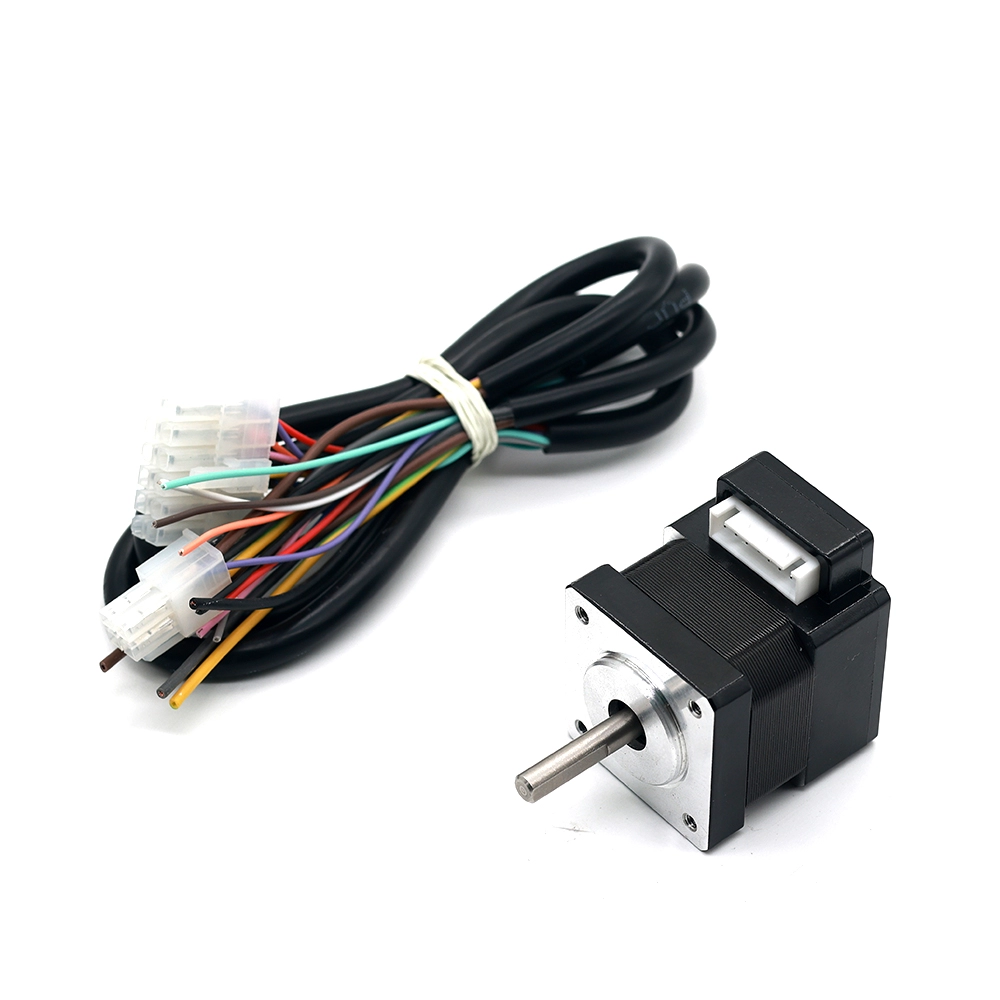
-
Encoder Feedback Issues
Reason:
closed loop stepper motors rely on encoder feedback to maintain position and speed. If there is an issue with the encoder or its signal, the motor may vibrate and fail to turn.
Solution:
– Check Encoder Connections: Ensure all encoder connections are secure and correct.
– Test Encoder Function: Use diagnostic tools to test the encoder’s functionality and signal quality.
– Replace Faulty Encoder: If the encoder is faulty, replace it with a new one.
-
Incorrect Motor Parameters
Reason:
Incorrectly configured motor parameters in the controller or driver can lead to improper motor operation, causing vibration without turning.
Solution:
– Review Motor Parameters: Check the motor parameters such as step angle, current rating, and operating mode in the controller or driver.
– Adjust Parameters: Adjust the parameters to match the motor’s specifications as provided by the manufacturer.
-
Poor Grounding and Electrical Noise
Reason:
Poor grounding or electrical noise can interfere with the signals sent to the stepper motor, causing erratic behavior like vibration without turning.
Solution:
– Improve Grounding: Ensure the motor and driver are properly grounded.
– Reduce Electrical Noise: Use shielded cables and keep signal cables away from high-power cables to reduce electrical noise interference.
-
Driver Overheating
Reason:
If the driver overheats, it might reduce the current to the motor to protect itself, which can result in the motor vibrating but not turning.
Solution:
– Check Cooling: Ensure the driver has adequate cooling, either through natural airflow, fans, or heat sinks.
– Monitor Temperature: Regularly monitor the driver’s temperature and ensure it operates within the recommended range.
Conclusion
Encountering a closed loop stepper motor that vibrates but doesn’t turn can be challenging, but by systematically diagnosing and addressing the common causes outlined above, you can resolve the issue effectively. Always start with the simplest solutions, such as checking the power supply and wiring, before moving on to more complex diagnostics like encoder feedback and driver settings. With a methodical approach, you can ensure your stepper motor operates smoothly and reliably, minimizing downtime and enhancing the performance of your projects.
Feel free to leave a comment if you have any questions or additional tips for troubleshooting closed loop stepper motor issues. Happy troubleshooting!